Dual-Track Online XLIN-VL-AOI68 AOI machine For Multiple Inspection And Control Positions Of SMT/DIP
● Concise and intuitive man-machine interface, in line with daily simple and effective operation habits.
● High-precision, high-resolution color digital camera, high-stability work to take pictures, restore real and natural image effects, and achieve high-quality image output. In theory, we can choose unlimited cameras.
● Telecentric lens (standard) High resolution, ultra-wide depth of field, ultra-low distortion and unique parallel light design, etc., can clearly image the tilt of the circuit board and tall components without squint.
● Comprehensive and flexible software, minimum training requirements, easy to use.
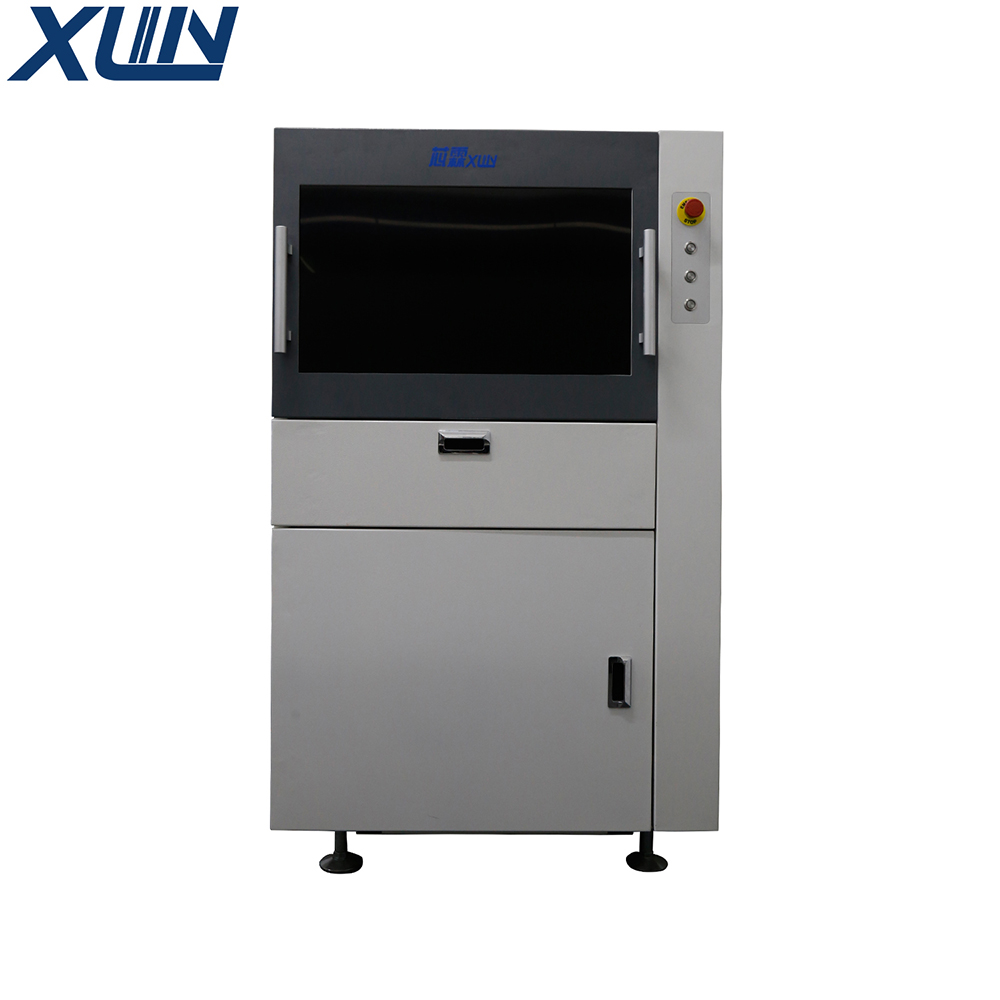
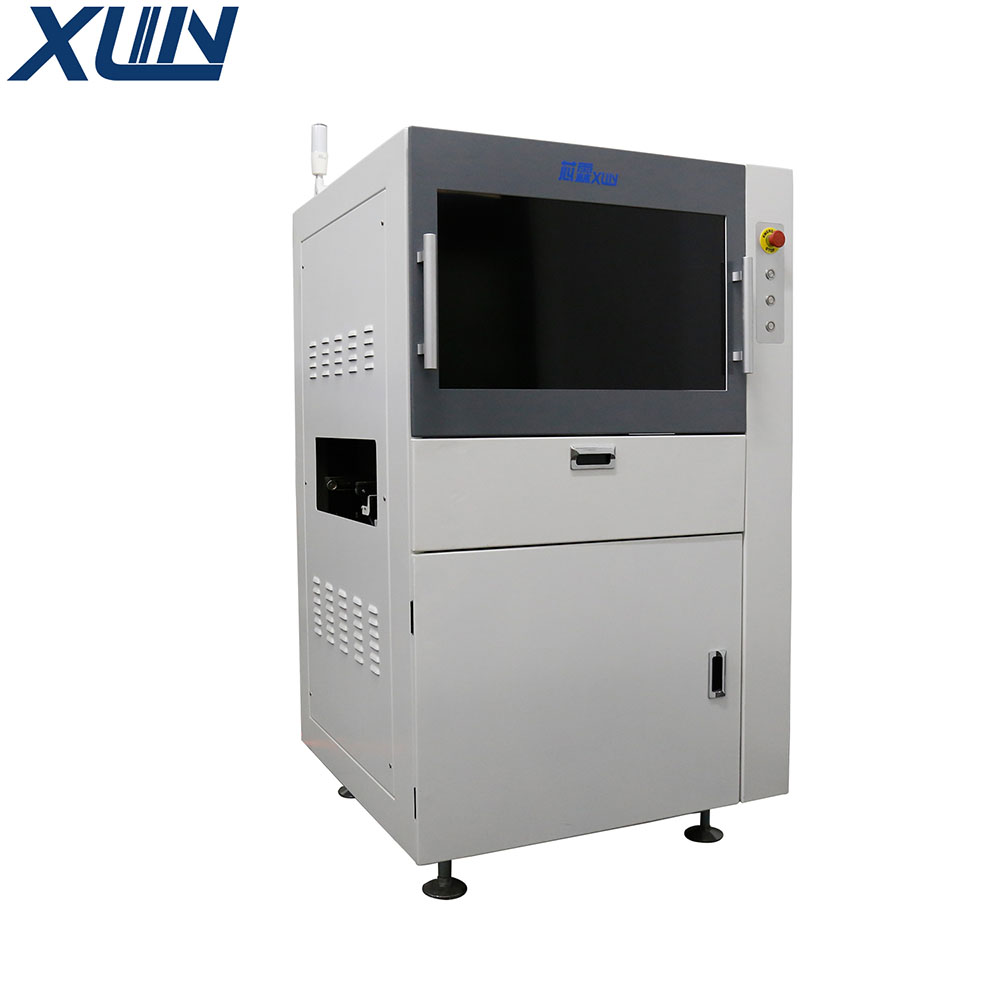
● Workflow wizard to keep the settings consistent.
● Convenient sliding door design makes maintenance more convenient.
● Large size detection range design, which can meet the detection requirements of different PCBs.
● It can cooperate with the OK/NG double receiving board connection station to truly realize the seamless connection of online testing, receiving board and maintenance, and support automatic connection with the front and rear equipment on the production line (online type).
● Off-line programming and application of off-line debugging function to maximize the utilization of equipment.
● Comprehensive application of a variety of practical algorithms, software application is more flexible.
● Using a mobile terminal under a wireless network, it is possible to set up workstations at any position in the workshop, adopting one-to-many mode, and confirm the detection data of multiple online machines through a maintenance workstation to achieve the purpose of saving personnel.
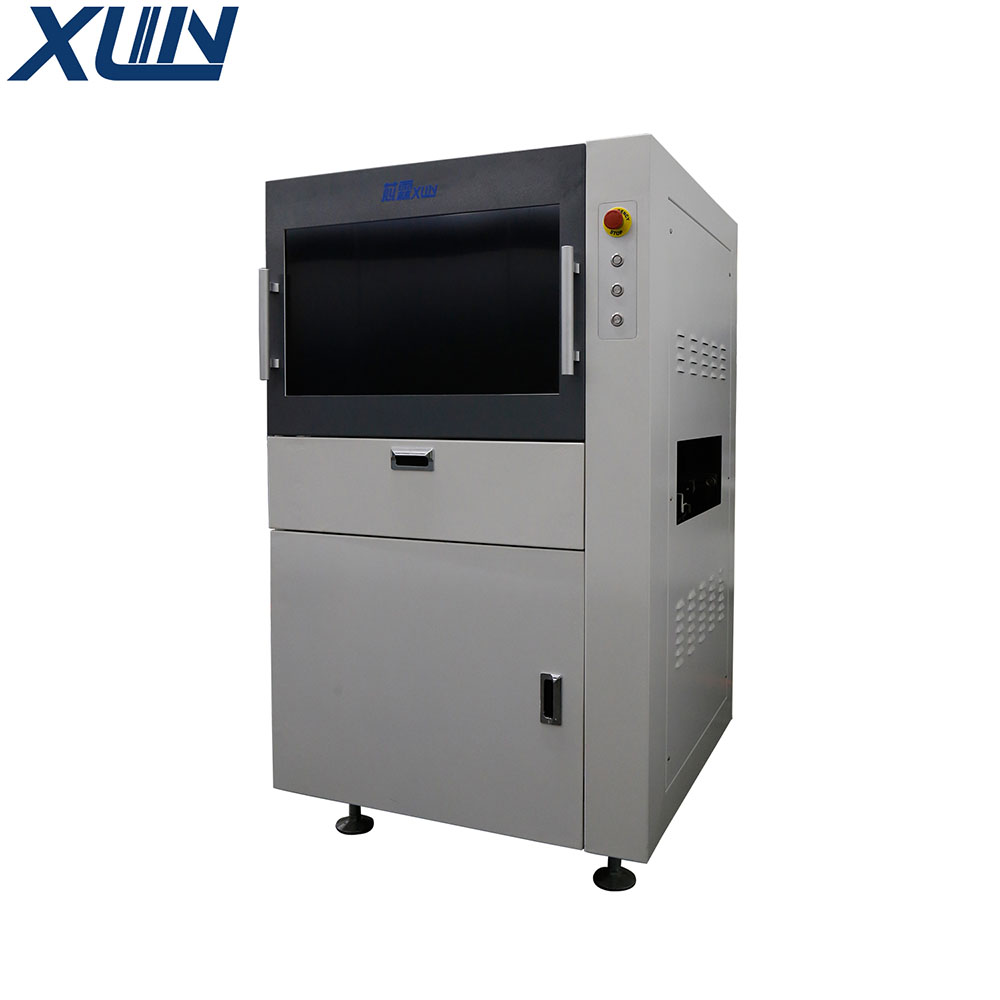
It can accurately prompt the exact defect name, and is supported by a complete SQL database system. It provides an SPC statistical analysis system in the form of pie charts and histograms, which is convenient for customers to perform process analysis and quality improvement.
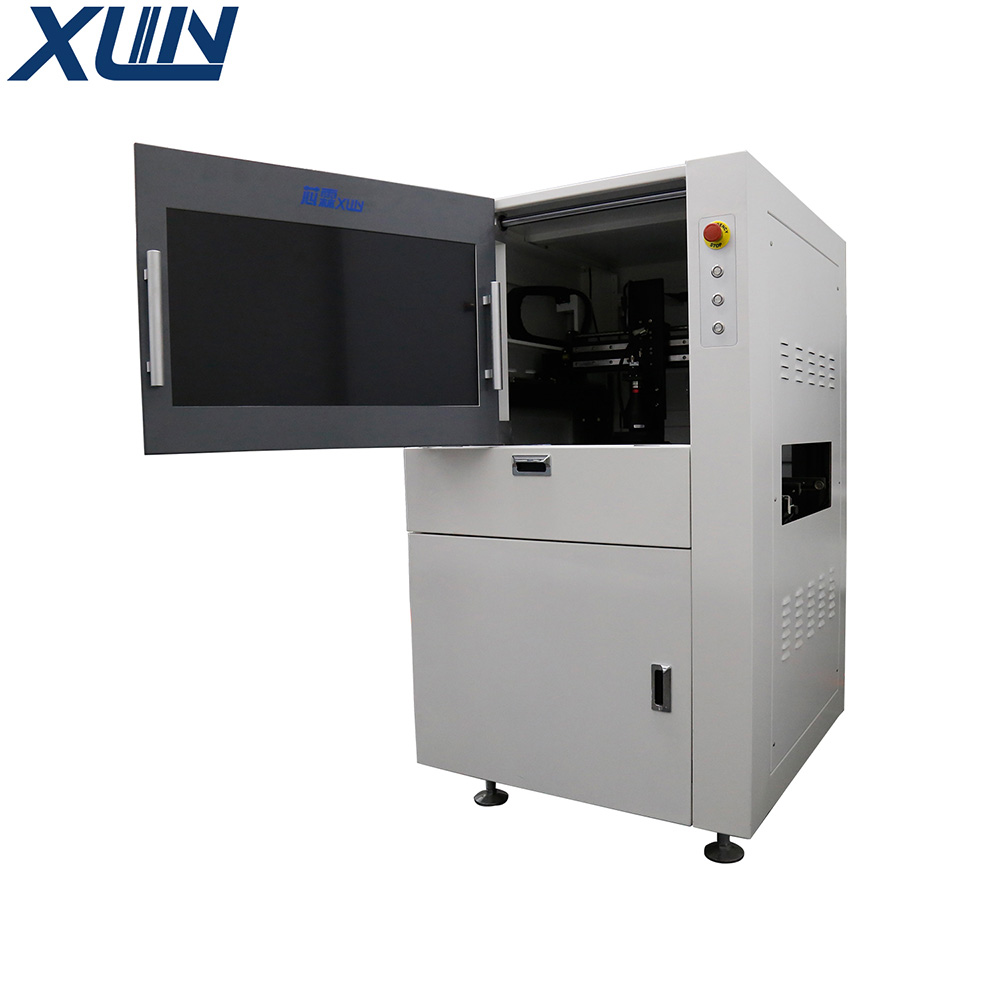
● Special response algorithms such as OCR character recognition and path testing can more effectively meet the quality inspection after printing, and the detection rate and pass-through rate are higher.
● Highly intelligent control system, real-time monitoring of product quality status and timely response.
● Realize the automatic linking of component standards through CAD, or the placement machine to import coordinate data to realize the automation of program design.
Circuit board tested | After SMT solder paste printing, before/after SMT reflow soldering, before/after DIP wave soldering, soft board, aluminum substrate |
Detection method | There are 26 algorithms involved in deep learning, vector analysis, color calculation, color extraction, grayscale calculation, image comparison, OCV/OCR, etc., and will continue to increase (template matching, intelligent detection, intelligent judgment, barcode recognition, two Dimension code recognition, character recognition, character verification, resistance value recognition, circle detection, polarity detection, scratch detection, bridge detection, average value, maximum value, minimum value, range value, local average value, brightness Extraction, relative offset, 2-end angle detection, collinearity detection, sub-component generation, calculated value, whole board detection [+], whole board detection [-], unilateral positioning) |
Camera | High-speed smart digital camera |
Camera/lens resolution | Camera: 5 million-20 million pixels, full-color high-speed industrial digital camera. We control the development of the source code, and theoretically can choose unlimited cameras. Lens resolution: 7um/10um/15um/20um/25um, and can be customized for special applications. Standard telecentric lens |
Light source | Depending on the application configuration of the ring three-dimensional multi-channel color light source, select the matching RGB specification and coaxial light source |
Programming mode | Manual writing, automatic search, CAD data import and automatic corresponding component library |
Detection coverage type | Solder paste printing: presence or absence, offset, less tin, more tin, open circuit, continuous tin, pollution, scratches, etc. |
Part defects: missing parts, multiple parts, offset, skew, tombstones, side standing, overturned parts, wrong parts, damaged, reversed, XYθ offset, etc. | |
Solder joint defects: too much tin, little tin, false solder, continuous tin, tin ball, glue overflow, no lead out, copper foil pollution, etc. | |
Special function | Automatically call the program, optimize the detection of the whole board, jigsaw and multi-mark, bad mark, multi-faceted simultaneous test. |
Minimum part test | 01005 chip, 0.3 pitch IC. Adjust the optical configuration according to the customer's process specifications |
SPC and process control | Record test data throughout the process, perform statistics and analysis, view production status and quality analysis, and export report formats such as Excel, Txt, and Word. |
Barcode system | Automatic barcode recognition (1-dimensional or 2-dimensional code), able to recognize large barcodes (multi-FOV smart splicing) |
Operating system | Windows 10 x64 operating system, Chinese or multi-language version, the latest operating system |
Check the result output | 32-inch LCD display, OK/NG signal |
PCB size range | Min: 50*50mm; Max: 460*650mm (single track mode); Max: 460*360mm for both tracks (single camera dual track mode). The fixed rails and moving rails defined by the front and rear equipment of the customer must be confirmed (normally 1 rail is fixed, 2-4 rails are adjustable), and can be customized for special applications |
PCB thickness range | 0.3 to 5 mm |
PCB clamping system edge clearance | Vacant within 3.5mm of the board edge |
Maximum PCB weight | 3KG |
PCB bending | <5mm or 3% of the diagonal length of PCB |
PCB top and bottom clear height | PCB (Top Side): 30mm PCB bottom (Bottom Side): 80mm |
Conveyor system | Bottom-up fixed, automatic compensation of PCB bending deformation, automatic in and out of the board, flat belt, automatic width adjustment |
Conveyor height from the ground | 880 to 920 mm |
Conveyor flow/time | It can be set to left→right right→left through the software. Time in/out of the board: 3-5 seconds |
X/Y platform driver | Driven by screw and AC servo motor, PCB is fixed, Camera moves in X/Y direction, each one has passed certification |
Power supply | AC220V 50/60Hz 1.5 KW |
Air pressure | 0.4~0.8Mpa |
Front and back device communication | Smema |
Equipment weight | About 750KG |
Equipment dimensions | L1000 (busy body length) * W1360 (without handle accessories) * H1660 mm, the height does not include the signal light. |
Environmental temperature and humidity | 5~35℃ 35~80% RH (no condensation) |
Equipment safety regulations | Comply with CE safety standards |
Optional | Repair station system, offline programming system, SPC server system, barcode recognition system, MES interface / Shop Floor interface |